“If something works this well, we’ll take two right away.”
The Challenge
A bakery products manufacturer approached us to reduce stretch film packaging costs andimprove pallet holding force, which had been leading to instability during transport.
Previously, manual wrapping was used, and each operator applied a different amount of film — typically around 400 grams per pallet. This inconsistency resulted in insufficient load retention, frequent pallet tipping, and damage during transportation, generating regular complaints.
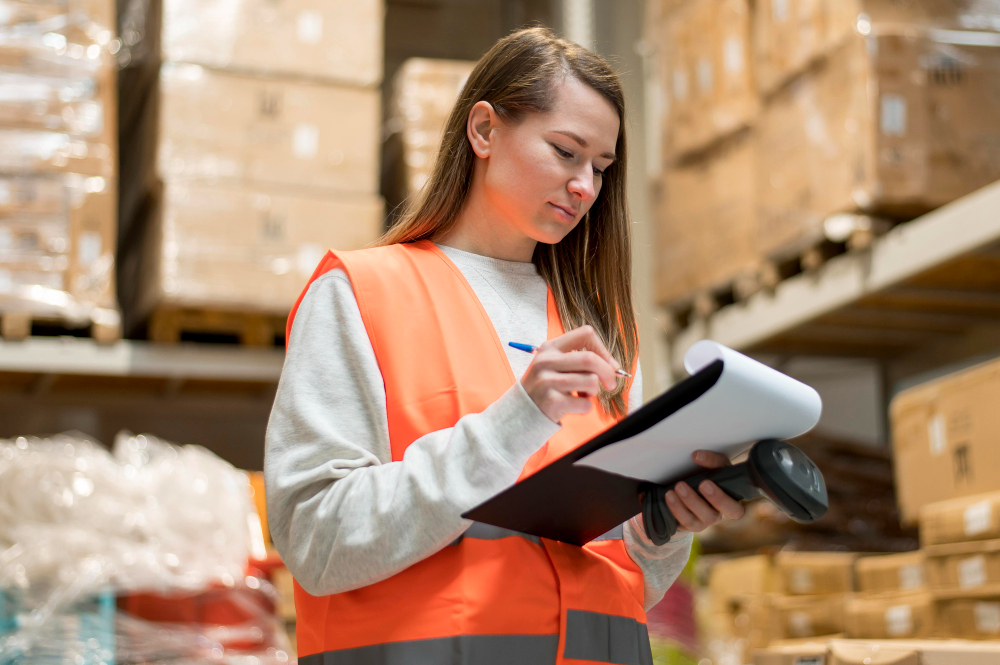
Our Proposal and Testing
Our team recommended switching to automated packaging, and after successful testing, the company moved forward with the investment. The result? A 70% reduction in film usage — now only 120 grams per pallet.
The Results: Stable Loads, Less Waste, Predictable Costs
- Consistent and secure pallet wrappingwith the same amount of film each time
- Significantly reduced unit costs thanks to film savings
- Monthly film savings: 336 kg
- Annual film savings: 4,032 kg
These impressive results convinced the management to purchase two packaging robots to fully implement the solution across operations.
Conclusion: Smart Packaging Pays Off
Automating the wrapping process resulted in lower material usage, enhanced load stability, and fewer damaged goods. This case shows that packaging optimization can be a real driver of business success.
📞 Interested in achieving similar results? Contact Gábor Arató at +36 30 682 60 50
📧 Email: iroda@manupackaging.hu
Let’s make your business more efficient – together!
— Gábor Arató, Managing Director, Manupackaging Hungary Kft.