A Partner Success Story
Our client, a plastic product manufacturer, previously relied on manual pallet wrapping. This approach posed several challenges: each employee used a different amount of film — between 400 and 600 grams per pallet — which not only led to inconsistent pallet stability but also caused frequent damage during transportation. Unstable wrapping resulted in tipping pallets and numerous customer complaints about broken products.
The Problem
- Manual wrapping led to inconsistent film usage (400–600 g per pallet).
- Pallets were often improperly secured, making them prone to tipping during transport.
- Frequent product damage and complaints were tied to inadequate packaging.
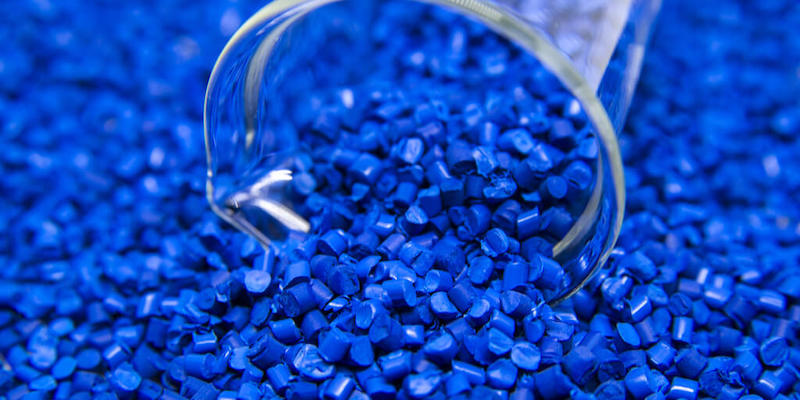
The Solution: Investing in Packaging Machinery
To address these challenges, the company decided to invest in a semi-automatic stretch wrapping robot (Sfera model). This upgrade provided:
- Consistent film usage, ensuring that each pallet received the exact amount of film required for proper load retention.
- Improved pallet stability, eliminating transport issues caused by poor wrapping techniques.
The Results: Efficiency, Savings, and Stability
- Stable Securing: The packaging machine applied a uniform amount of film per pallet, guaranteeing reliable retention and eliminating pallet tipping during shipping.
- Film Savings: The previous manual wrapping required around 400 g of film per pallet, while the automated process only needed 120 g — a significant material reduction.
- Cost Reduction: The reduced material usage and fewer damaged goods led tomajor cost savings.
Key Figures
- Monthly film savings: 336 kg
- Annual film savings: 4,032 kg (72% reduction)
- Packaging speed: 60 pallets per day
- Payback period: The machine paid for itself within 8 months
- EPR Fee savings: HUF 551,880 saved within 6 months due to reduced packaging waste
Return on Investment
Thanks to the efficiency gains and EPR savings, the investment in the wrapping machine paid off within just 8 months — and even faster when considering reduced fees alone. This change translated into a leaner, more sustainable packaging operation.
Conclusion
Introducing automated packaging not only enhanced operational efficiency but also significantly reduced packaging costs. With consistent film usage and improved pallet stability, the company not only minimized product damage but also improved transport safety and sustainability.
Let’s Make Your Business More Efficient – Together!
– Gábor Arató, Managing Director, Manupackaging Hungary Kft.